QR Code manufacturing
The manufacturing industry employs a dynamic and highly mobile workforce. With QR Code, you can monitor field employees, track activities and tasks performed in the field, track your manufacturing processes, and collect real-time data in your warehouses using mobile devices. Employees can use smartphones or tablets for easy QR code scanning, completing mobile forms, tracking manufacturing processes through their various stages, and data lookup.
QR codes also help track employee hours, overtime, shift changes, mileage, equipment usage, associated tasks and adherence to safety protocols.
Sign Up for Free Trial
Use of QR Codes in Manufacturing
-
Monitor Employees and Tasks
-
Track Tasks and Equipment
-
Employee Punch In/Out
-
Inspections of the Product and Process
All manufacturer orders/product batches are identified by QR code or barcode. Shop floor employees scan QR code/barcode with the mobile device to access and record information. Employees handling work orders can immediately see what steps were completed, what step the work order is on, which QR inspection form(s) are already filled out and which tasks need to be done. All this information is available by scanning the QR code/barcode label on the work order. |
![]() |
Equipment used in manufacturing must follow the equipment code to adhere to certain quality standards and protocols in ensuring the safety of the equipment being used. However, verifying manufacturing equipment and materials may typically be a cumbersome process. By embedding a URL link to a maintenance website into the QR codes used on heavy-duty and non-heavy duty manufacturing materials, businesses can ensure that tools, equipment and materials are being used correctly so as to minimize errors. |
![]() |
QR code can be used to punch In/Out workers as and when they arrive at the manufacturing facilities by simply scanning the QR code at the job site. If workers forget their mobile phone, or for those who don’t have one, Crew Punching enables supervisors to check them in, either individually or as a group. Workers who may forget to punch-in or punch-out when they arrive at the job-site or in the evening when they get off, can trigger an alert that will notify the supervisor and will help to address this issue. |
![]() |
By using QR Code for inspections, you can monitor your product levels, build the product according to the order, track your manufacturing processes, and collect real time inspection data in your warehouses using mobile devices. Employees can use smartphones or tablets for easy QR code scanning, completing inspection forms, tracking manufacturing processes through their various stages, and data lookup. Information collected using mobile devices is sent to a secure, central cloud location and is instantly available to all authorized users. |
![]() |
Benefits of QR Code for Manufacturing Industry

Product/Order inspection
Product/Order supervisors can scan the tasks being completed and also collect any type of inspection data – notes, tasks, signatures, pictures or use custom forms. View data in real-time or generate automatic reports. And trigger alerts on each scan.

Real time visibility
Provides complete visibility into manufacturing workers. Supervisor/Admin can see the locations of all workers on a map in real time, enabling them to monitor manufacturing operations and make sure that they are working at the right location and on the right tasks.

Early Punch In/Out Prevention
Workers will not be allowed to punch In/Out early or from different manufacturing sites and pretend to be at the job site. Supervisor/Admin will be notified about this, helping improve the overall efficiency of the team.

Works on all Smartphones
alGeo’s QR Code apps work on any smartphone.

Rules and Reminders
If workers forget to punch in/out, the allGeo rule based system can set up reminders to workers if they forget to punch in/out.

Workers Safety
Monitor and ensure workers’ safety while they are at the manufacturing job sites. Workers can manually trigger a safety alarm via the mobile app. Or set up a customized proactive safety-check workflow to monitor and detect any threats. Supports multi-level back office threat escalation using IVR, SMS and/or email.

Reports & Analytics
Generate scheduled and on-demand location breadcrumb reports. Tells you where your workers have been and which ‘worksites’ they worked during the day.

Works Offline
allGeo QR code app for manufacturing works in areas with poor network connectivity or no network at all. When workers enter into a good network area, data will be automatically synced up.

Two Way Communication
With allGeo QR Code app, the Supervisor/Admin can communicate with workers while they are at the job-sites and vice-versa.
Leading Brands we have worked with
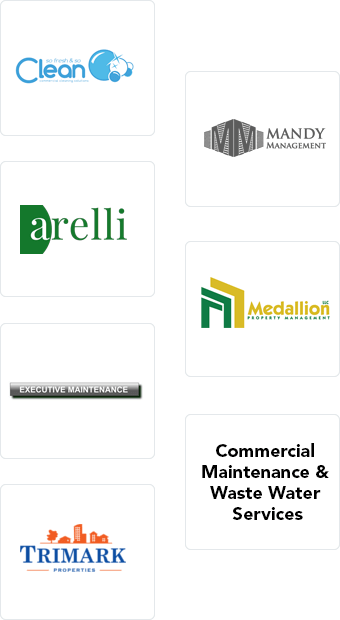
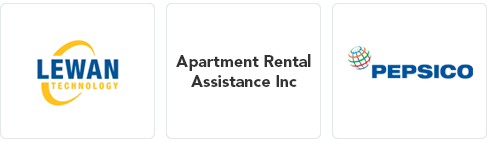
The allGeo solution
help our supervisors better manage their teams, but the new myTeam tools also allow our
field employees to collaborate more effectively in real time
With allGeo I can
see where my crew is whenever I need to, and add an extra level of accountability. We have
been able to improve delivery times, cut operating costs and increase the number jobs we
complete per month.
allGeo has
completely automated the payroll process for us. Our backoffice does the adjustments to job
sites and schedules from the web portal on the fly and it seamlessly works for everyone in
the field. allGeo has shaved off at least 50% of our payroll processing tasks.
With allGeo we've
been able to improve our customer response time and save time and money by pinpointing 100%
of our manpower on a map at a glimpse.
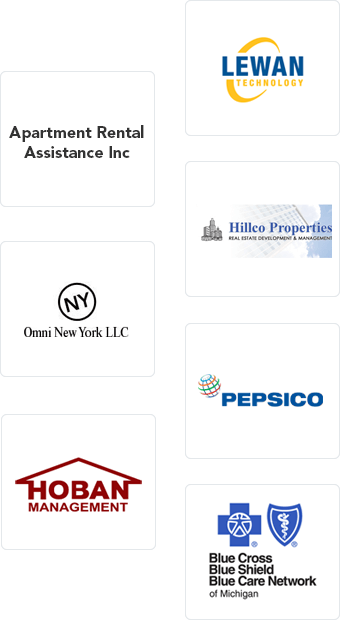
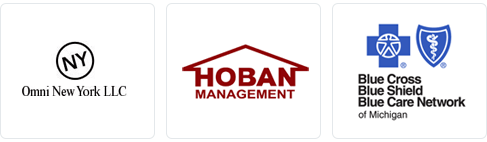
How does allGeo QR Code App work
The App works via a Mobile App. The Employees need to install the app from the App Store and complete the registration process.
Once the mobile number is registered, the manager/admin needs to set up the schedule in the system.
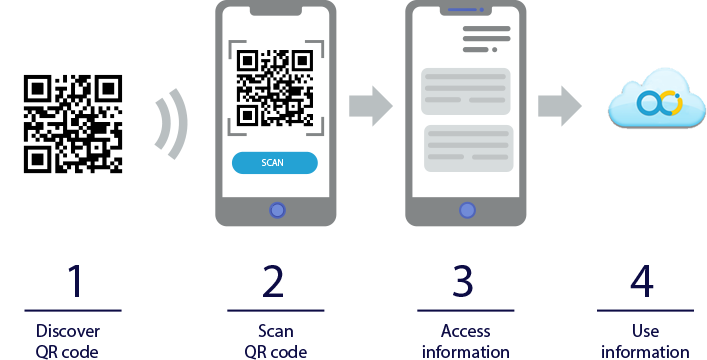
QR Code Workflow
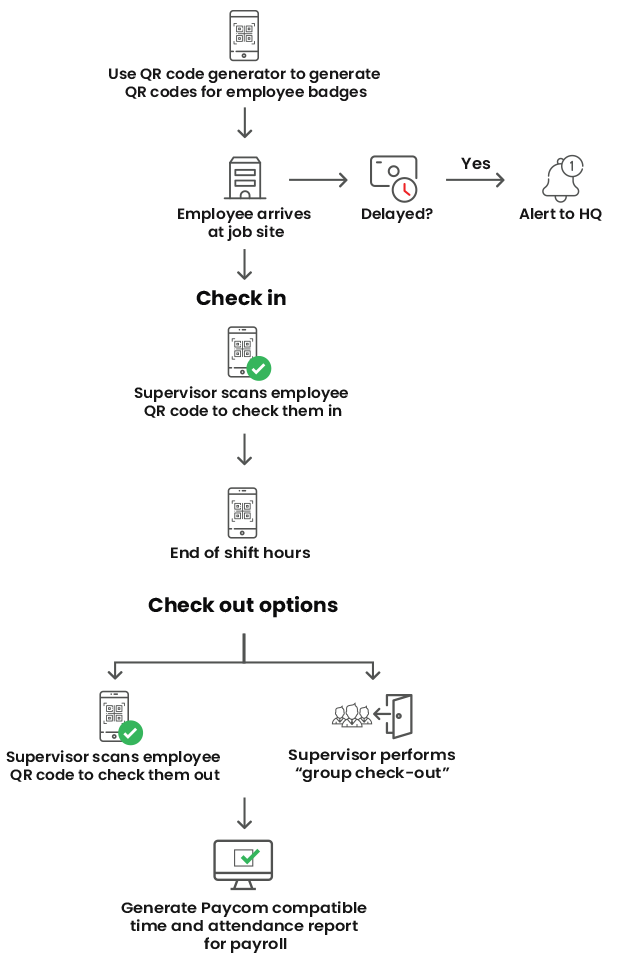
Activate Your 14 Days Free Trial Now!
No commitment | No Credit Card |Required Assured Savings
Get Started